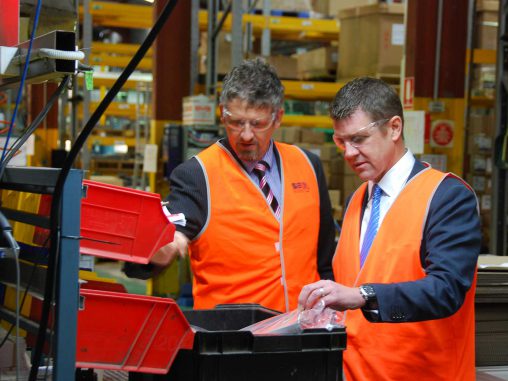
Seeley International is bucking the trend of manufacturers closing their Australian operations by upgrading its existing factory in Albury to bring in-house the production of heating components that were previously externally sourced.
The fully automated tube bending cell was officially opened earlier this month at the company’s Albury factory, where more than 120 people are employed, involved in the production of Braemar gas heaters and air-conditioners.
Seeley International founder and executive chairman, Frank Seeley said the business is proud to have been a major employer in the area for more than 20 years, which will be further supported by manufacturing the heat exchanger tubes for ducted heaters on the premises.
Seeley said the opening of this new manufacturing cell reinforced the company’s passionate belief that local manufacturers can effectively offset the higher employment and production costs experienced in Australia by focusing on innovation, using world class technology and embracing high levels of automation.
“These components were being externally sourced from a supplier that was using imported tube, and escalating production and supply costs meant having to consider sourcing them offshore — but our manufacturing process has reduced costs, taken the quality to an even higher standard, and kept this work in Australia,” Seeley said.
“I am delighted that after more than 12 month’s hard work and an investment exceeding half a million dollars, we have created this highly automated tube bending cell to complement our existing manufacturing operations.”
The manufacturing process is describes as: “one end former, two tube benders and three robots all working in perfect unison to transform pipes of varying lengths and diameters so that they fit perfectly into a premium quality, highly energy-efficient heat exchanger.”
“Bringing this process in-house will create additional jobs as our sales continue to grow, and it is anticipated that our commitment to continuous innovation will result in this technology ultimately producing many other components for our various gas heaters,” he said.